The Canadian Space Agency - STEAR Program
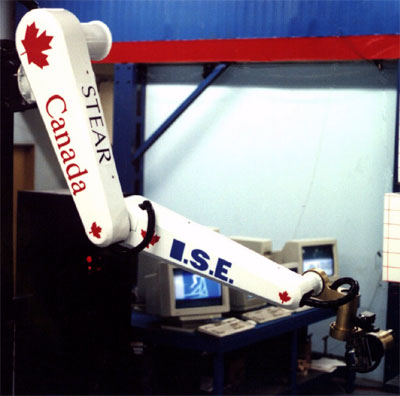 |
The STM System is a ground-based robotic testbed facility developed for the STEAR (Strategic Technologies in Automation and Robotics) program. It is a kinematically identical version of the SPDM (Special Purpose Dextrous Manipulator) built by Canada for the International Space Station. The STM System forms the core of the CSA's CART (CSA Automation and Robotics Testbed) facility , which is used for:
- Development of space station work tasks
- Testing of robot technologies
- Control methodologies
The STM System consists of two seven-degree-of-freedom, 7 ft. long manipulators, each provided with a control computer. It also includes a machine vision system and a workstation to act as a high level operator interface and a testbed server. |
Each of the STM manipulators has one EMDC (embedded module for distributed control) for each actuator. The EMDCs use a 68332 microcontroller for control algorithm processing and a transputer for data communications. Each actuator can be controlled in position or force control mode. The actuators are based on brushless DC motors with harmonic drives.
The Manipulator Control Computers are PCs on a Windows NT platform, each with a plug-in card with two C40 DSPs. ISE's ACE control software runs on the PCs and DSPs. The Manipulator Control Computers provide:
training
trajectory generation
reactive obstacle avoidance
impedance control
cartesian control
joint level control
They can be controlled by a local operator or by the Testbed Server workstation.
The Testbed Server is an SGI Indigo 2 workstation. It provides 3D graphical displays, high level operator commands, and automatic path planning. The server also controls access to the STM System to external control computers.
The STM actuators, controllers, and software modules can be used in other custom electric manipulators.
ISE SPDM Testbed Manipulator (STM) is kinetically identical to the dual arm 7 degree of freedom Special Purpose Dextrous Manipulator (SPDM) that will fly on Space Station Alpha. The electric STM is built in either single arm or dual arm configurations.
- The STM reach is 2 metres
- The payload for the STM is 14 Kg in the presence of gravity
- The accuracy of the STM using computer vision feedback is .125 mm. Without vision the accuracy is 6 mm
- Unload endpoint velocity is .1 m/sec (min) in any direction
STM is equipped with the "Integrated Robot Controller". A significant aspect of this controller is that it provides to the STM impedance control capability. Therefore, the STM can interact with its environment with stability. This allows the STM to effectively perform, for example, insertion tasks. |
|
|